EVolution EMC
The EVolution EMC cable gland – developed for the most demanding electromobility applications
EMC technology simplified!
AerosUSA has devoted a great deal of attention to the topic of electromobility. In this broad field, high currents often occur in the motor supply cables, which, due to the high switching frequencies from the DC/DC converter, also burden the high-voltage vehicle electrical system with high-frequency interference.
At the same time, the demands on the connection tightness and ease of installation of the products used are very high. The EMC cable glands available on the market in the past managed to fulfil individual requirements, but never to satisfy all the particular needs of electromobility applications.
The latest result of AerosUSA’s product development efforts in this area is the new, high-quality EVolution EMC cable gland, which is easy to use and characterised by high functionality, efficiency and reliability – pushing the boundaries of what could be expected from such products in terms of performance and practical applications.
The highlights of the EVolution EMC cable gland
- Design allows pre-assembly on cable
- “Pluggable” EMC contact solution
- Significantly faster and safer installation on the vehicle
- Process reliability from harnessing to installation
- Design supports maintenance (e.g. replacement of sealing insert)
- Lead-free brass (lead content < 0.1% – complies with future RoHS directive)
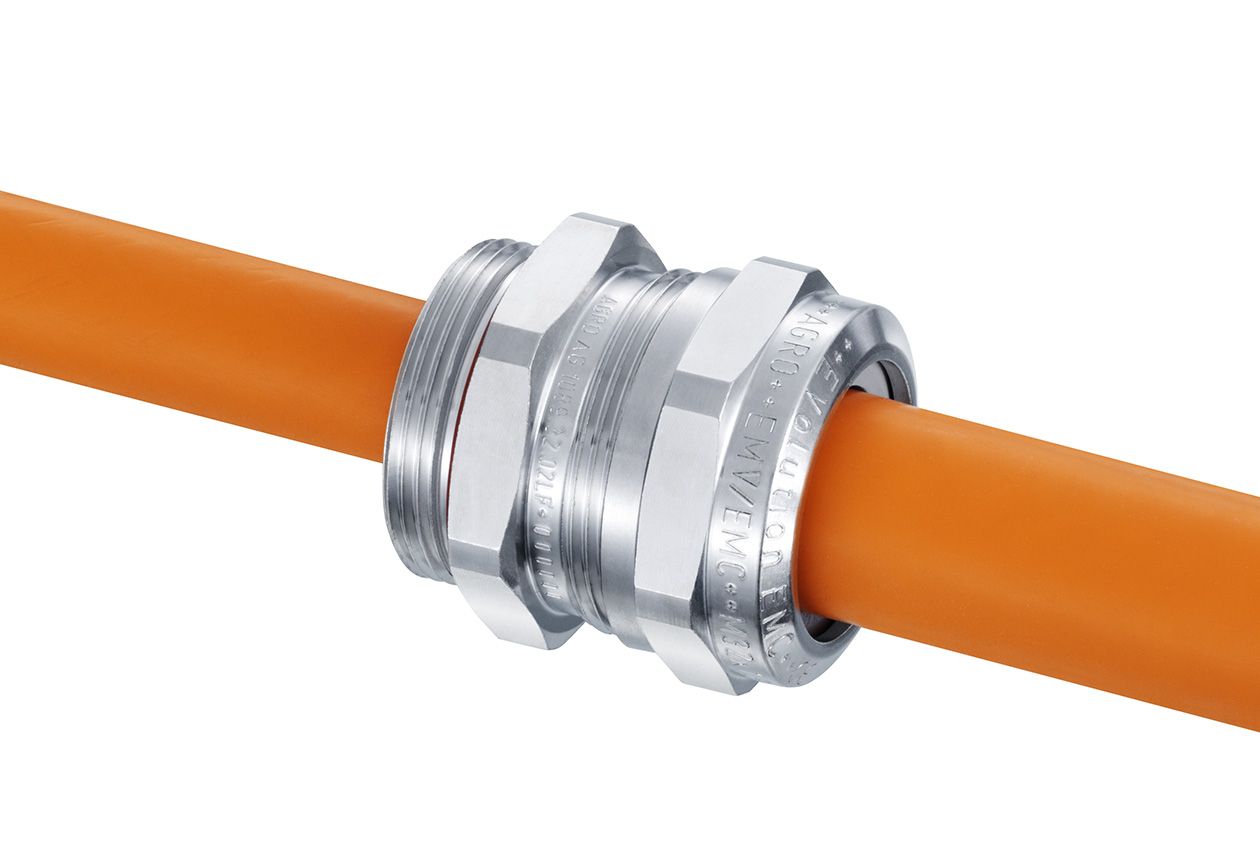
The EVolution EMC is not a typical EMC cable gland as known from industrial applications. In fact, it is very different – the best of both worlds:
A top-quality cable gland, but easily disconnectable. Quick and easy to use, yet designed for the highest shielding currents, for all high-voltage cable types and for all engine-power classes. During maintenance work, the sealing insert can be replaced without having to disconnect the cable. And during preparation for installation, the high-voltage cables can be pre-assembled with this EVolution EMC cable gland, like a plug, enabling them to be connected to the vehicle in the fastest possible way. A torque wrench is not even required for this, and the connection tightness is still ensured. As easy as possible, and as safe as it has to be in the automotive industry.
Pre-assembly on the cable is carried out safely and reliably using the practical, cordless, hand-held AXI-PRESS tool. Regardless of whether done during cable fabrication or during installation on the vehicle, the crimping of the shield contact sleeve can be carried out in a matter of seconds. A data interface ensures traceability, as does the batch number marked on each EVolution EMC cable gland. As a result, a level of process and product reliability is achieved that surpasses what was ever possible with any other cable gland.
Megatrend mobility: Transition to electric drive systems
In the ongoing transformation of mobility towards CO2-neutral drive systems, hybrid or fully electric vehicles are undoubtedly at the center of the action.
Where the vehicles are batter powered or of the fuel cell type, e-mobility is a megatrend of today’s world. All market segments are affected by this transition to a new future.
Expert knowledge of EMC cable glands
![]() |
Life-long reliabilityIn relation to reliability and service life, the EMC shield contact of high-voltage cables in electric vehicle applications is often not given enough attention. In addition to the shield current carrying capacity, the sum of all loads in service has a significant influence on the product’s service life and thus on its performance. It is too often assumed that a new vehicle’s ability to meet all specified EMC requirements, particularly in relation to the components of the EMC shield contact, means that it will continue to do so throughout the vehicle’s service life and in all operating conditions. But, in fact, EMC tests are only required for new vehicles, and how the EMC values of the high-voltage vehicle electrical system will change over the service life remains uncertain. If a power component in a vehicle’s drive train fails, this is immediately noticeable in the system as a malfunction. If an EMC shield contact fails, however, the situation is very different. In such a case, the operational reliability of the vehicle is drastically affected, with EMC interference emissions from damaged or destroyed shield contacts. These “interference sources” can cause EMC coupling at “interference sinks” in other locations, e.g. on control lines or in electronic components. The various possible impacts on control signals represent a latent reliability risk. Furthermore, troubleshooting the problem – including finding the interference source and the interference sink in the workshop – typically requires great effort and is very costly. And to resolve the problem, it is not uncommon for extensive changes to be made to the EMC protection concept – changes that usually affect not just one vehicle but an entire fleet. With the EVolution EMC® cable gland, these costs can be saved. It is clearly more economical to allow for the use of high-quality EMC cable glands right from the start, rather than subsequently carrying out time-consuming and expensive troubleshooting and/or using expensive monitoring devices. |
Five steps to assemble the EVolution EMC
Process-safe cable assembly – an important part of planning Pre-assembly of HV cables with standard industrial EMC is not process-reliable enough in e-mobility to permanently guarantee completely secure functioning of the cable glands in commercial vehicles or construction machinery. The EVolution EMC was precisely tailored during development to meet these requirements, enabling accurate specification of the shield contacting and the individual work steps. These few steps ensure that the cable shield cannot be damaged or displaced after assembly. A close-fitting and strong hold on the cable is achieved. As it is completely crimped between the support sleeve and the contact sleeve in this new solution, no shield strands can break out. This prevents a potential short-circuit hazard in the component housings. In addition, it is no longer necessary to apply heat shrink tubing or tape to fix the shield end although having heat shrink does always provide an extra element of support. |
![]() |
![]() |
Process reliability
In the manufacture of individual devices, vehicle components, subassemblies and entire vehicles, process reliability is generally the top priority – especially in the context of any shortage of skilled workers. It is therefore essential that proper attention be paid during selection of EMC cable glands to their process-reliability during cable assembly, installation on the vehicle, and any subsequent removal and reinstallation (maintenance work). A strong focus was placed on these aspects in the development of the EVolution EMC cable gland. The EMC contact system must be assembled on the cable using the AXI-PRESS tool, in accordance with the instructions. The process enables the user of the EVolution EMC to plan for the steps to be carried out semi- or fully automatically. The final assembly on the vehicle has also been redesigned and significantly simplified with regard to safety and reliability. For vehicle and machine manufacturers, the benefits include improved process reliability, increased operational reliability and lower installation costs. 1. Push the cable lug through
|